The Importance of Defoamers in Industrial Processes and Applications
The Importance of Defoamers in Industrial Processes and Applications
Blog Article
Choosing the Right Defoamer for Your Particular Application Requirements
Picking the appropriate defoamer for particular application demands is a nuanced procedure that demands cautious factor to consider of several elements, such as the foam operating, tool, and kind problems. Recognizing the nuances of defoamer performance-- including rate and determination-- while additionally accounting for governing and ecological factors is essential. Furthermore, participating in tests and seeking advice from makers can supply useful insights. Browsing these complexities can be complicated, and the consequences of a poor selection might be substantial. What methods can be employed to make sure an optimum choice?
Comprehending Foam Formation
Foam development occurs when gas is caught within a fluid, creating a stable framework of bubbles. This sensation can significantly impact different commercial processes, specifically in markets such as food production, drugs, and wastewater treatment. The existence of foam can prevent blending, lower product high quality, and also result in operational inadequacies.
Foam generally forms as a result of a combination of aspects, including surface-active agents, anxiety, and the attributes of the fluid stage. Surfactants lower the surface area stress of the fluid, promoting the formation of bubbles that can stabilize and integrate. Frustration, whether from mechanical stirring or gas intro, boosts bubble development, leading to increased foam quantity.
Comprehending the mechanics of foam formation is critical for sectors intending to enhance their processes. By determining the certain conditions that promote foam generation, organizations can carry out methods to reduce its results. This understanding lays the foundation for picking proper defoaming representatives that successfully target the special obstacles presented by foam in various applications. A thorough understanding of foam development is vital for improving performance and preserving item integrity throughout numerous markets.
Kinds of Defoamers Available
Different kinds of defoamers are offered to resolve the challenges positioned by foam in industrial applications. defoamers. Generally classified, defoamers fall under 3 categories: silicone-based, non-silicone-based, and natural defoamers
Silicone-based defoamers are renowned for their effectiveness and security throughout a wide variety of temperatures and pH degrees. They are typically utilized in applications where solid foam reductions is required, such as in layers, paints, and adhesives. Their low surface stress permits quick foam collapse.
Non-silicone-based defoamers, often made from organic substances, supply an alternative for applications sensitive to silicone residues. These defoamers can be additional separated into polyether and ester kinds, each tailored to meet particular formula demands. Non-silicone defoamers are frequently made use of in food processing and individual treatment items because of their compatibility with numerous formulations.
Natural defoamers, originated from plant or animal sources, are getting grip because of their green account. These items are particularly appealing in applications where regulatory conformity and sustainability are extremely important, such as in agrochemicals and biotechnology.
Choosing the from this source best kind of defoamer is important for enhancing efficiency and guaranteeing compatibility with particular applications.
Secret Application Considerations
When picking a defoamer, it is vital to consider the details application demands to make sure ideal performance. defoamers. Various sectors have unique requirements, such as food processing, drugs, or wastewater therapy, and each application may require one-of-a-kind defoaming residential or commercial properties
Secret elements to assess include the medium in which the defoamer will certainly be used, whether it is water-based, oil-based, or a combination thereof. The temperature and pH degrees of the application can also significantly affect the efficiency of a defoamer. Additionally, compatibility with other chemicals existing in the system is critical to stop unfavorable responses that could compromise efficiency.
Another vital factor to consider is the lathering actions of the particular system. Recognizing whether the foam forms promptly or slowly can lead the selection of a defoamer that targets the root reason effectively. The preferred speed of defoaming can influence the selection, as some applications require rapid activity while others might tolerate slower defoaming processes.
Lastly, regulative and environmental considerations need to not be neglected, especially in sectors with stringent conformity requirements. Selecting a defoamer that lines up with these aspects guarantees check over here both efficiency and safety and security in the application.

Efficiency Screening Approaches
Assessing the performance of a defoamer calls for an organized approach to testing that accurately measures its efficiency in certain applications. Different performance screening approaches can be used to establish the ideal defoamer for a given solution.
One common approach is the bubble examination, which evaluates the defoamer's capacity to view website reduce foam quantity over time. This test entails creating a steady foam and after that adding the defoamer to observe the price of foam collapse.
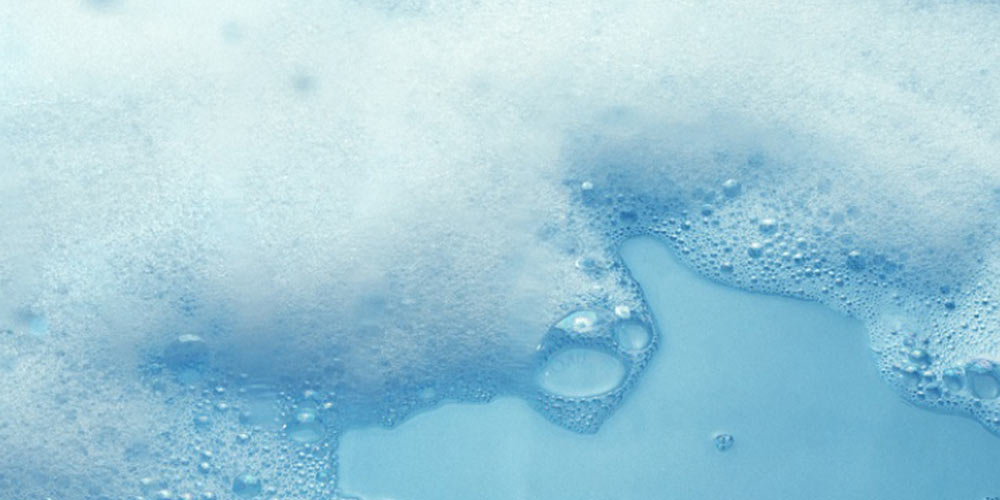
Inevitably, picking the suitable efficiency screening technique depends upon the certain application and the type of foam being attended to. Each technique uses useful data that can direct formula adjustments and enhance the effectiveness of the defoamer in practical applications.
Ideal Practices for Option
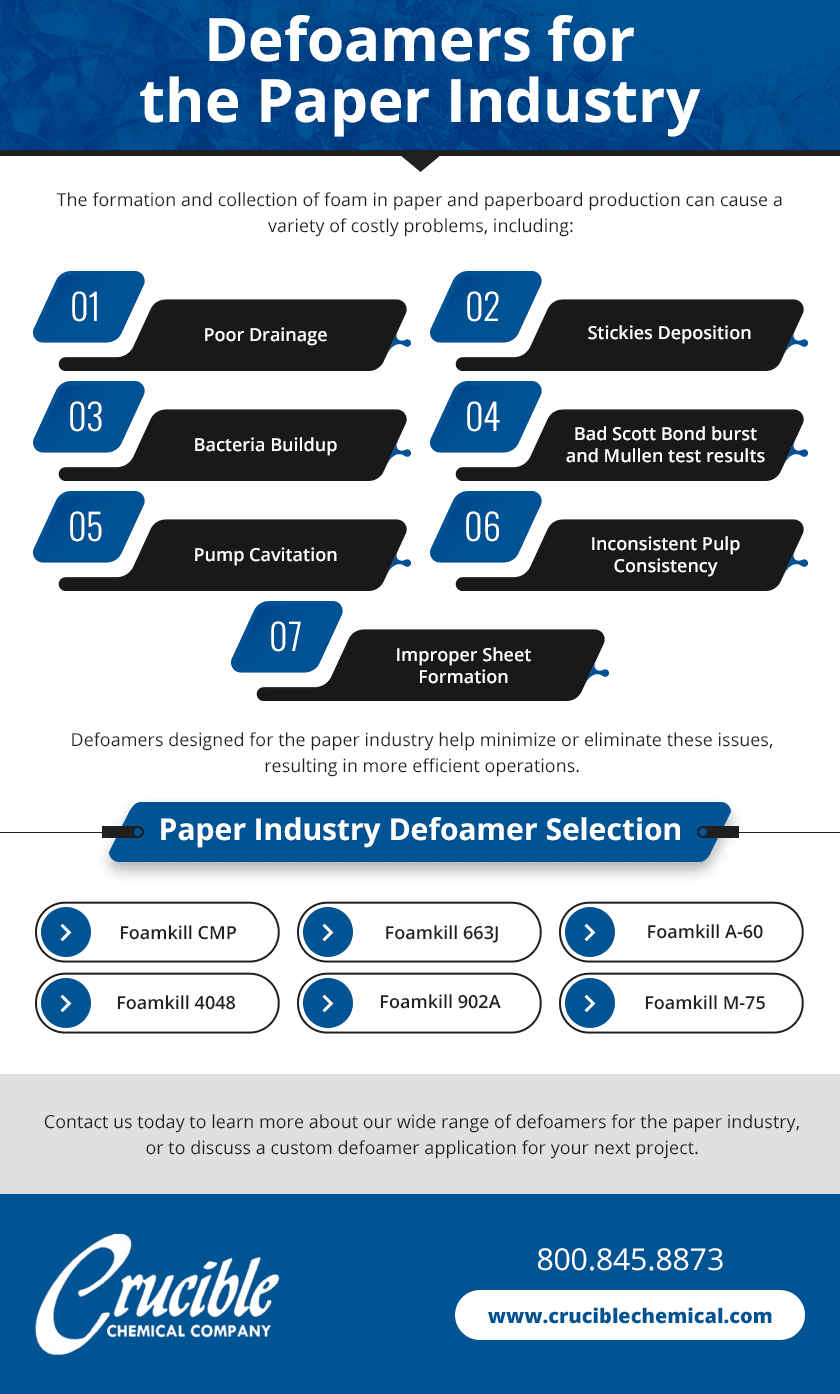

Following, consider the defoamer's efficiency in terms of rate of action and persistence. A quick-acting defoamer might be required for processes where fast foam suppression is important, while an extra relentless solution could be required for long term foam control. In addition, review the ecological influence of the defoamer, including its biodegradability and any type of regulatory compliance demands.
Conduct tests with chosen defoamers to identify their performance in real-world problems. By adhering to these best techniques, you can improve foam control efficiency and ensure the durability of your procedures.
Verdict
In recap, picking the proper defoamer requires a thorough assessment of different aspects, including foam type, medium, operating conditions, and ecological considerations. Recognizing the unique attributes of foam development and the offered defoamer alternatives is crucial.
Selecting the proper defoamer for certain application requirements is a nuanced procedure that requires mindful consideration of several aspects, such as the foam tool, kind, and operating conditions.Choosing the ideal defoamer is critical for attaining ideal performance in foam control applications. A quick-acting defoamer may be required for processes where quick foam reductions is essential, while a more persistent formula might be needed for long term foam control.In summary, picking the appropriate defoamer demands a detailed analysis of various elements, consisting of foam kind, tool, operating problems, and environmental considerations. Comprehending the distinct features of foam development and the available defoamer options is crucial.
Report this page